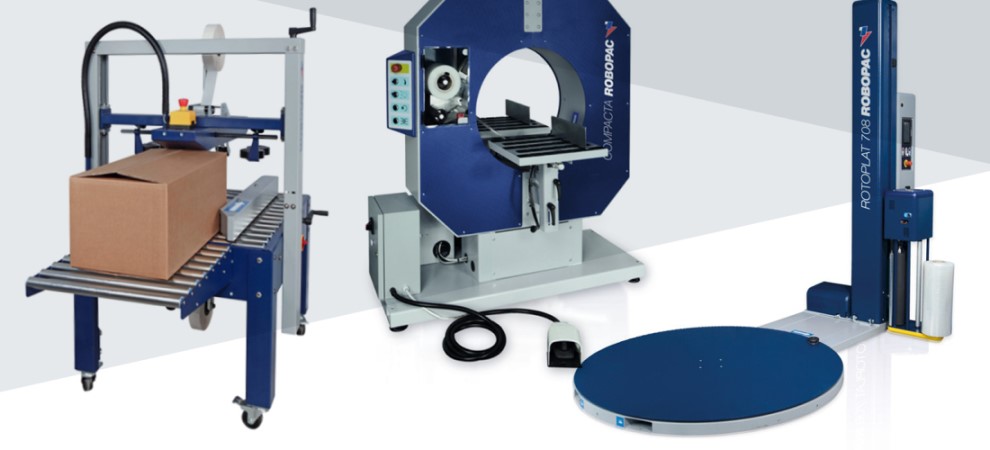
Packaging equipment: Lease and try before you buy!
Purchasing packaging equipment can be a major investment for your company. How can you be sure you’re investing in the right equipment? By leasing before you buy! Take advantage of this option available at CARTIER.
You’ve already determined that investing in packaging equipment is essential for growing your business. But you still hesitate. Is it the right time from a financial perspective? Will you choose the right equipment for your needs?
Instead of putting off a decision that could potentially generate big returns in terms of efficiency and savings, why not start by leasing the packaging equipment you’re interested in?
This service is now available through CARTIER, which offers a broad range of packaging equipment under its lease-before-you-buy program.
4 reasons to lease equipment before buying
At CARTIER, we’re confident that investing in packaging equipment can dramatically improve the efficiency of your packaging processes.
However, since this can be a major investment, you naturally want to ensure you make the right choice. This is precisely why we offer you the option to lease equipment before you buy.
By leasing, you can:
1. Confirm efficiency and profitability
- If you’re seeking to increase the production volume of your packaging processes but aren’t yet convinced that a particular piece of equipment will help you save significant time, leasing provides an opportunity to verify that the return-on-investment scenarios presented are realistic.
- You can confirm at the same time that you will use significantly less stretch film. For example, stretch film savings can reach 30% to 55% for wrapping machines equipped with Cube Technology.
- If it’s necessary to convince your management team that investing in packaging equipment is profitable, then leasing provides an opportunity to demonstrate a machine’s advantages and justify its purchase.
2. Verify equipment integration
- By leasing, you can ensure that the equipment in question is effectively adopted by your team. Employees are occasionally hesitant to embrace automation for fear that the equipment will take away their jobs. Leasing gives them a chance to try out the equipment and quickly realize that the technology simply makes their jobs easier.
- If you aren’t sure whether you have enough available space to accommodate a turntable, for example, then leasing will provide you an opportunity to try out this machine in your own environment.
- You can also take advantage of leasing to familiarize yourself with the equipment technology, especially if you’ve never used these types of machines before.
3. Ensure that equipment meets your requirements
- If you’re wondering whether a particular machine meets your packaging needs, leasing provides the opportunity to find out under actual conditions while working with your own products.
- By testing equipment for one or two months, you can find out whether it is suitable for all potential packaging scenarios at your facility.
4. Use leading-edge equipment
- If your current budget doesn’t allow you to invest in the purchase of packaging equipment, leasing can provide you access to top-quality equipment while also turning a large initial outlay into a small monthly payment.
These are not the only scenarios where leasing is the best option. If you have any doubts as to whether leasing is the right choice for you at this time, or if you can’t decide between purchasing or leasing, we’re here to help.
Contact a CARTIER Account Manager today or visit our equipment leasing page.
The Cartier team also suggests
Equipment
Categories: Écoresponsabilité, Equipment
Revolutionizing packaging with paper!
Investing in automation and betting on innovative equipment is exciting! But it doesn’t happen overnight. If you have the motivation and drive to make a change, don’t hesitate to contact us. You’ll could be among the pioneers who choose greener options.
Equipment
Categories: Equipment
ERGONOMICS AT WORK, WHY GO WHITHOUT!
The well-being of your employees at work is a critical issue for most companies: among other things, it motivates employees to perform their tasks as well as possible. In times of labor shortage, it becomes even more important to take care of your employees in order to keep them for a long time. With few employees in the job market and multiple offers, they can afford to raise their expectations. This is why working conditions are becoming primordial, and why employers are trying to differenciate themselves from each other. It is possible to improve these conditions in several ways, starting with adapting the various workstations to make them ergonomic and safe. Here’s how to improve the ergonomics of your work place to reduce the risk of musculoskeletal disorders (MSDs) among your teams.
Equipment
Categories: Equipment, Technical
Most popular equipment used by manufacturers
Shortage of labor being greatly felt in most industries, many of our clients decide to go for automation to save time but also to reduce work pressure on their current employees. We cannot deny the fact that the greater the need for manpower, the more employees have to fill this gap by working harder. Therefore, many companies decide to invest in automatic or semi-automatic equipment. Obviously, some machines are more popular than others, for several reasons. Very often, semi-automatic equipment is the first choice of clients as the initial investment is lower.