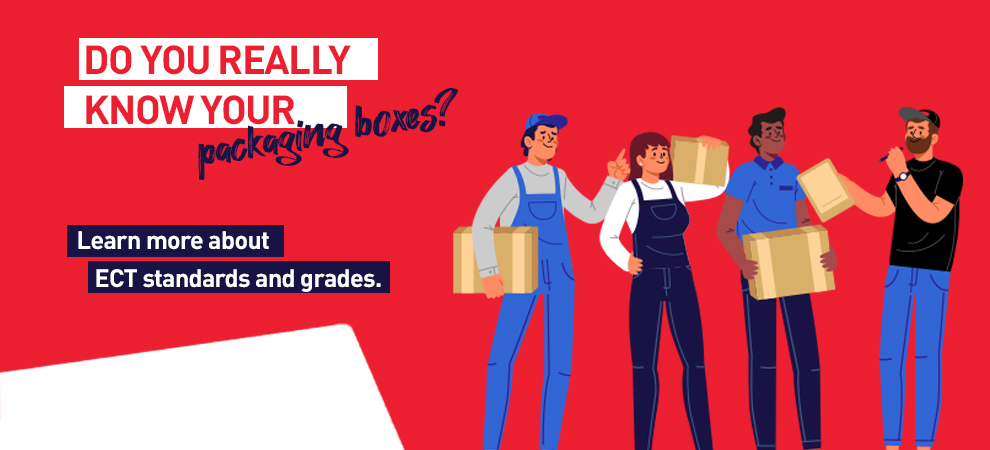
Do you really know your packaging boxes?
How about learning more about the corrugated cardboard that makes up the famous boxes? You may be surprised by this material that you thought was easy and free of any certification.
Packaging means boxes! Small, large, wide, flat, they all have one thing in common: the corrugated cardboard used to make them.
How about learning more about corrugated cardboard? You might be surprised by this material, which you thought was easy and free of any certification.
Far from being a young man, corrugated cardboard was patented in North America… in 1871! Packaging and protection: its functions are much the same as those we know today. What has really evolved is its composition, which has gone from two layers (liner and medium corrugated paper) to three (plus liner), in order to make it more solid.
Unfortunately, delicacy was not at the heart of the concerns of the time. Often tossed unceremoniously into train carriages, the boxes may have been sturdier, but they couldn’t prevent breakage due to handling.
To their rescue? Super standards!
How can we counter the ever-increasing incidence of breakage? By adopting quality standards such as the Mullen norm. Its objective? To increase the shatter resistance of our beloved boxes. And how? Thanks to a design based on fibers running in all directions. The result? Well… but there’s room for improvement. While resistance to bursting has indeed increased, the same cannot be said for resistance to vertical compression, aka the pressure exerted by boxes stacked one on top of the other.
Instead of being discouraged, the field adopted the ECT standard, which made vertical compression its battlefield! The fibers are arranged in the same direction, making them more resistant to crushing.
The cardboard commonly used in packaging is therefore identified by the acronym ECT for “Edge Crush Test”. How do you do? But what does it mean? Associated with a number between 23 and 55, it’s an identification grade that indicates the vertical compression force per linear inch, or more simply, the strength of the famous cardboard. For example?
If a box has an ECT32 grade, it means it can withstand at least 32 pounds per linear inch. In other words, the higher the grade, the heavier the load it can support.
Okay, but how is the grade determined? Several factors come into play: weight and size of contents, storage and handling conditions. Once you’ve determined the grade, you also need to consider the width of the flutes. The wider they are, the more likely they are to puncture. So, if you’re looking for a printed box, you’ll want to avoid cardboard with wider flutes.
In other words, if two customers have the same product to package, they won’t necessarily choose the same cardboard, because everyone has their own needs and constraints! That’s why it’s so important to get to know your packaging boxes, to know whether they can really satisfy your needs.
How to qualify the grade of cardboard? By a test of strength – or rather by a crushing resistance test – which you now know under the name ECT. The overall principle consists of supporting a load on a ring of cardboard. If it breaks between 32 and 39, the grade will be ECT32. To get the next grade, the ring must break at 40. Sometimes rings break at 39.6! And that’s not enough to get the precious higher grade. This explains the variations in resistance within the same grade.
48%: this is the loss of force in vertical compression of a box on its 180th day of storage. And between you and me, this is not such a rare situation! Stacking your boxes is much more technical than it seems!
“May the force be with you… and in your corners”! Indeed, it is in the corners of a box that we find the most force, at a rate of 20% in vertical compression each. You understand that positioning one corner of a box in the center of another is not a very good idea since it increases the risk of crushing.
4 Commandments, 0 Risks is the solution for stacking boxes and creating more stable, durable pallets:
|
![]() |
Who would have thought that behind a simple corrugated cardboard box, there was so much thought involved? In addition to learning design details, you’ve certainly learned that taking the time to choose your boxes properly is important.
When it comes to packaging, nothing should be left to chance, including the quality of the cardboard. Well-packed parcels and well-stacked pallets save time and money! And that’s crucial for companies like yours.
So, if you’re ready to improve the way you do things, our experts are here for you!
The Cartier team also suggests
Products
Categories: Products
Shipping marathon? Not a problem with CARTIER!
The time of year when online orders explode is coming! Fortunately, CARTIER is here to support you and lower your stress level. How can we help? By providing you with exactly the boxes and shipping packaging you need, and by optimizing your shipments.
Products
Categories: Écoresponsabilité, Products
PCR or how to reuse and perform with CARTIER!
Les marques qui choisissent le PCR contribuent à fortement réduire les déchets dans les décharges. Eh oui: opter pour le PCR, c’est diminuer l’extraction de matière première naturelle non renouvelable, et donc amoindrir l’impact sur les écosystèmes.
Products
Categories: Products
CARTIER your partner for Shipathon!
Whether you’re a distributor or a retailer, take advantage of our game strategy to establish a flawless game plan and beat your competitors to the punch!